Pigging Returns: Measuring the Value of Pipeline Efficiency in Industrial Operations
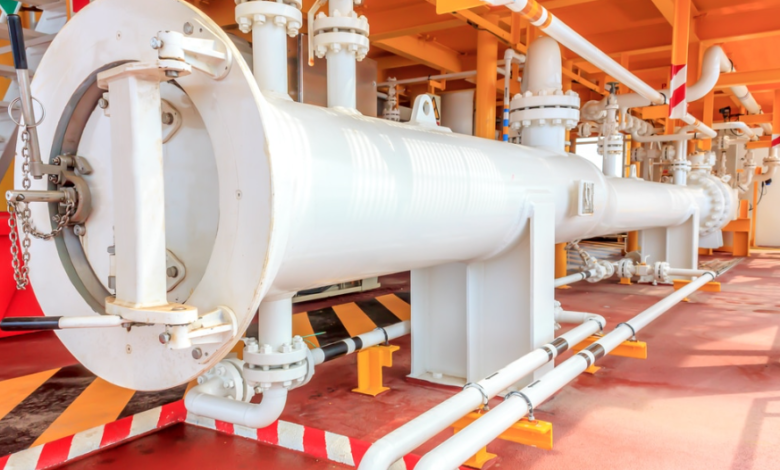
In a world where every drop counts—whether it’s product, water, or time—industries are under immense pressure to improve efficiency, reduce waste, and boost profit margins. Among the technological advancements helping businesses achieve these goals, pigging systems stand out as highly effective tools. But for many stakeholders, the key question remains: What kind of pigging returns can we expect?
From product recovery to downtime reduction, pigging systems offer a wide range of operational and financial benefits. This article explores the concept of pigging returns, examining how different industries measure and maximize the gains associated with pipeline pigging.
What Is Pigging?
Pigging refers to the practice of sending a device—known as a “pig”—through a pipeline to clean, clear, or recover leftover product between production runs. Initially developed for the oil and gas sector, modern pigging systems are now widely used in the food and beverage, cosmetic, chemical, and pharmaceutical industries.
Today’s pigging systems are advanced, often automated and integrated with control systems, allowing businesses to reduce product loss, increase hygiene, and save on cleaning time and resources. But most importantly, they provide tangible pigging returns that justify their installation and maintenance.
Defining Pigging Returns
Pigging returns refer to the measurable financial and operational benefits gained from implementing a pigging system. These returns are realized through various channels, including:
- Recovery of valuable product left in pipelines
- Reduced use of cleaning agents and water
- Less production downtime during changeovers
- Lower labor costs and manual intervention
- Prolonged equipment lifespan
- Enhanced compliance and reduced contamination
In simple terms, pigging returns are about getting more value from every production cycle, while minimizing waste, time, and costs.
See also: How Technology is Transforming Logistics in Hong Kong
Product Recovery: The Primary Pigging Return
Perhaps the most obvious and direct source of pigging returns is product recovery. Pipelines often hold several liters of product after a batch transfer. Without pigging, this residual product is usually washed out and discarded—resulting in significant financial loss.
Real-world example:
A plant producing personal care lotions might lose 15–30 liters of product per batch in its pipelines. If the lotion sells for $10 per liter, that’s $150–$300 lost per batch. With 300 batches a year, pigging can save $45,000 to $90,000 annually.
Even modest product recovery can dramatically impact the bottom line, making product recovery a cornerstone of strong pigging returns.
Cleaning Cost Reductions
Cleaning between product runs requires water, chemicals, energy, and labor. Pigging systems substantially reduce the need for lengthy cleaning cycles by removing most residual material mechanically.
Estimated savings:
- Water usage: Reduced by 60–90%
- Cleaning chemicals: Reduced by 50–80%
- Cleaning time: Reduced by 40–70%
- Wastewater disposal: Greatly minimized
Combined, these savings contribute to both operational efficiency and environmental compliance, delivering ongoing pigging returns beyond the production floor.
Reduced Downtime Equals Higher Throughput
Changeovers and cleaning cycles take time—time when the line isn’t producing. Pigging reduces these interruptions, meaning production can resume faster.
Example:
- Traditional cleaning time per changeover: 45 minutes
- Pigging-assisted cleaning time: 15 minutes
- Time saved: 30 minutes × 200 changeovers/year = 6,000 minutes or 100 hours/year
- With labor and overhead costs at $50/hour, that’s $5,000 saved annually—per pipeline
That’s without counting the opportunity cost of lost production during those 100 hours. Faster changeovers mean more batches completed, higher throughput, and ultimately, better pigging returns.
Equipment Protection and Lifespan Extension
Residue buildup in pipelines can lead to corrosion, contamination, and damage to equipment like pumps and valves. Pigging keeps pipelines clean and reduces abrasive wear, leading to:
- Fewer repairs
- Less maintenance downtime
- Lower replacement costs
While harder to quantify upfront, these savings reduce total cost of ownership (TCO) and contribute to longer-term pigging returns.
Case Study: Pigging Returns in a Sauce Manufacturing Facility
Scenario:
- 100-meter pipeline for transferring tomato paste
- 25 liters of product lost per run
- Product value: $6/liter
- 350 runs/year
Without Pigging:
- Lost product/year: 25 × 350 = 8,750 liters
- Financial loss: 8,750 × $6 = $52,500
With Pigging:
- 95% recovery = 8,312 liters
- Recovered value: $49,872
Additional savings:
- Cleaning chemicals: $5,000/year
- Downtime reduction: $3,500/year
- Labor savings: $2,500/year
Best Practices to Maximize Pigging Returns
To ensure you get the highest possible return from your pigging system, follow these expert tips:
✅ Assess Your Needs Accurately
Different industries and product types require different pigging solutions. A custom-designed system will always outperform a one-size-fits-all approach.
✅ Automate Where Possible
Automated pigging systems reduce human error, optimize timing, and boost efficiency. Though initial costs may be higher, returns are significantly greater over time.
✅ Maintain Your Equipment
Like any mechanical system, pigging equipment must be properly maintained. Regular servicing ensures consistent performance and uninterrupted returns.
✅ Monitor KPIs
Track product recovery volumes, cleaning time saved, utility use reductions, and waste metrics to measure actual pigging returns and make adjustments as needed.
Conclusion: Pigging Returns Make the Case Clear
Implementing a pigging system is more than just a technological upgrade—it’s a business decision with long-term financial, operational, and environmental rewards. By reducing waste, recovering product, saving time, and enhancing compliance, pigging systems deliver real, measurable value.
As industries move toward leaner operations and sustainability-driven models, those who invest in pigging technology are already reaping the benefits. And with pigging returns proving consistent and strong, it’s not a matter of if you should invest—but how soon you can start seeing the value flow back to your bottom line.